Noggrann bearbetning av cylinderlopp för lastbilsmotorer med recessingverktyg
Framgångsrikt samarbete mellan användare, maskintillverkare och Mapal. Moderna lastbilsmotorer tillverkas vid Mercedes-Benz fabrik i Mannheim. Kraven för bra motoregenskaper inkluderar extremt snäva toleranser för de vitala måtten på motorblocket. Tack vare det nära samarbetet mellan specialister från Mercedes-Benz, maskintillverkaren och MAPAL, gjordes betydande framsteg när en ny produktionscell för bearbetning av motorblock utformades.
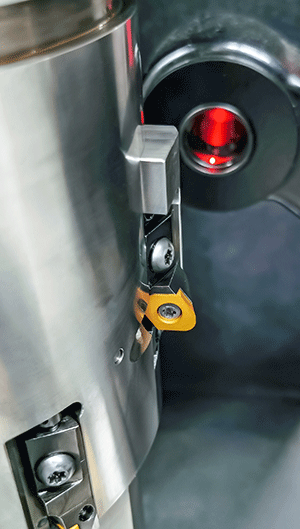
Vid tillverkning av motorer krävs högsta precisionsnivå. För att säkerställa bästa möjliga motoregenskaper måste ytorna som bearbetas göras med högsta möjliga noggrannhet. De har en komplex geometri och ett flertal nyckelegenskaper (KC) för vilka de högsta toleransklasserna måste uppnås på ett tillförlitligt sätt. Beroende på motortypen, måste flertalet H7 toleranser uppnås, flertalet områden med noggrannhet som är mindre än 15 μm liksom faser med snäva toleranser, inklusive en utgång med 20° fas, som har en vinkeltolerans på endast
± 0,025 ° (1 ’ 30 ”) måste uppnås samtidigt som de höga kraven på ytkvalitet tillgodoses. Förutom noggrannhet, är fokus också på kostnadseffektiv tillverkning.
Detta är endast möjligt med ett recessingverktyg
Den första produktionscellen för dessa motorblock togs i drift 2011. När man planerade en andra produktionsenhet använde de ansvariga teknikerna sina erfarenheter från den första produktionslinan. De identifierade att bearbetningen av hålen för cylinderfodren som särskilt utmanande. Bearbetningen var uppdelad i två stationer: en förbearbetning och en finbearbetning.
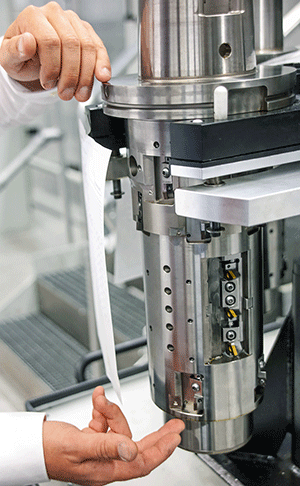
För detta ändamål har MAPAL utvecklat komplexa recessingverktyg som är bestyckade med upp till 20 vändskär, både ISO-skär och kundanpassade skär. Recessingverktygen har en verktygskropp i monoblock design. HSK160-anslutningen har en större plankontakt med en diameter på 200 mm. Ett verktyg väger upp till 60 kg. Oavsett kopplingen och en verktygslängd på 380 mm måste man se till att verktyget har en rundgångs-noggrannhet på 3 μm. Sliderna manövreras med en dragstång via en extra NC-axel i maskinens styrsystem. Dragstången måste integreras i HSK-kopplingen för att vara lämpad för automatisk verktygsväxling. Denna utmaning löstes med en bajonettkoppling med hög precision, som används för att koppla dragstången automatiskt under en verktygsväxling.
Inuti verktyget överförs dragstångens rörelser till sliderna med hjälp av hårdmetalls skenor. För att uppnå de önskade volymerna bearbetas tre hål samtidigt med tre spindlar. De tre verktygen per maskin är tilldelade till en viss spindel, vilket säkerställer processenssäkerhet. För varje verktyg finns ett systerverktyg, och ett ytterligare reservverktyg så man kan sköta regelbundet underhåll och renoveringar hos Mapal.
Med tanke på att verktygen måste tillverkas med stor precision, är den manuella tillverkningen hög hos MAPAL. Som t.ex. glidaxlarna i verktygskroppen är läppade för hand, och noggrannheten i dragstångsmekaniken ska uppfylla de högsta kraven när det gäller precision gör att den manuella arbetstiden för var och en av dessa verktyg uppgick till flera arbetsveckor.
Skärbyte och justering av verktyget utanför maskinen
Med bearbetningsoperationer som dessa justeras och byts skären i maskinen. På grund av kylmedlet är detta inte bara obehagligt för maskinoperatören, maskinen kan inte heller producera under denna tid. I 3-skiftdrift och med tre verktyg per maskin, kan detta driftstopp kunna uppgå till tre till fyra timmar per dag. Tillsammans med de anställda från Mercedes-Benz och maskintillverkaren utvecklade Mapal därför ett koncept för automatisk verktygsväxling för att justera verktygen utanför maskinen. Detta kan låta elementärt först, eftersom det är det normala förfarandet för denna typ av bearbetning. I det här fallet visar dock enbart de olika dimensionerna på verktygen bli en stor utmaning. Med tanke på att en maskin med automatisk verktygsväxling för denna typ av bearbetning och dessa dimensioner är den första i världen, krävde projektet en hel del innovativa idéer och oräddhet att prova nya synsätt från alla i projektet.
Unik inställningfixtur för vertikalt hängande verktyg
För att göra inställningen utanför maskinen den så enkel som möjligt och med säkert resultat utvecklade MAPAL motsvarande anordningar för att transportera, justera och underhålla verktygen. En hanteringslösning behövdes för att sätta in och ersätta verktyget i magasinet, eftersom verktygen är insatta i bearbetningssystemet medan de hänger, vilket är ganska ovanligt. Eftersom verktygsvikten är på cirka 60 kg, är det en kraftansamling för operatören att bara ”vrida över” verktyget två gånger manuellt, när man arbetar med en sådan vikt spelar säkerhetsaspekten också en viktig roll. Risken att skada verktyget i processen är också överhängande. Det är därför MAPAL utvecklade två unika inställningsfixturer där verktygen sätts in i en hängande position. En vagn för hängande transport mellan maskinen och inställningsfixturen utvecklades också. Verktygen transporteras och justeras därför i samma position som de används i maskinen.
Mätresultaten som bestäms på inställningsfixturerna sänds direkt till ett RFID-datamedium på verktyget. Styrenheten för maskinen läser av informationen när verktygen sätts in i maskinen igen. På så sätt kan maskinen justera några av de viktiga måtten med hjälp av recessing under bearbetningen. Från och med det andra arbetsstycket beaktas resultaten av den rutinmässiga QA-mätningen. Denna slutna kvalitetskontroll-loop för verktygen var en hög prioritet för Mercedes-Benz.
Sammantaget beställdes produktionslinan som planerat. Verktygen fullgör sina uppgifter i enlighet med alla specifikationer, och motorblocken tillverkas nu med stor precision på produktionslinan.
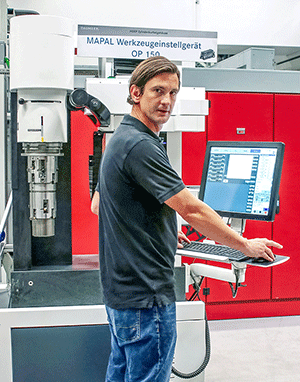
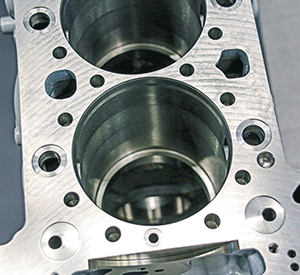
Hittar du inte vad du söker?
